Choice of turning amount
The Tungsten Carbide Inserts programming of Tungsten Carbide Inserts machine tools reflects the programmer's process intention through the program. How to choose the turning amount reasonably plays a key role in the processing economy of the parts and the formation of the final precision of the parts. For Tungsten Carbide Inserts Manufacturer, the amount of turning should be selected economically; for rough machining, the amount of turning should be selected according to the machining accuracy of the parts, especially the surface roughness.
The cutting quantities in Tungsten Carbide Inserts include: back engagement ap, spindle speed S or cutting speed VC (for constant linear speed cutting), and feed rate VF or feed rate f. These parameters should be selected within the allowable range given by the machine tool.
1. Determination of the amount of back cutting ap (ie depth of cut)
When the rigidity of the process system and the power of the lathe allow, the ruler may choose a larger amount of back cutting to reduce the number of feeds, improve the production efficiency, and at the same time reduce the loss of the machine tool (mainly the backlash of the lead screw) influence on machining accuracy. The economical CNC machine tool that adopts stepper drive for the feed servo system must avoid the phenomenon of out-of-step caused by excessive depth of cut.
2. Determination of spindle speed
Spindle Speed for Smooth Surface Turning Spindle speed should be selected according to the selected back force, feed and tool durability. Generally, it can be calculated according to the empirical formula, and according to the practical experience of production, you can refer to the manual selection of the cutting amount within the cutting speed range allowed by the machine tool manual. It should be noted that the low-speed output torque of the AC variable frequency speed control CNC machine tool is small, so the cutting speed cannot be too low.
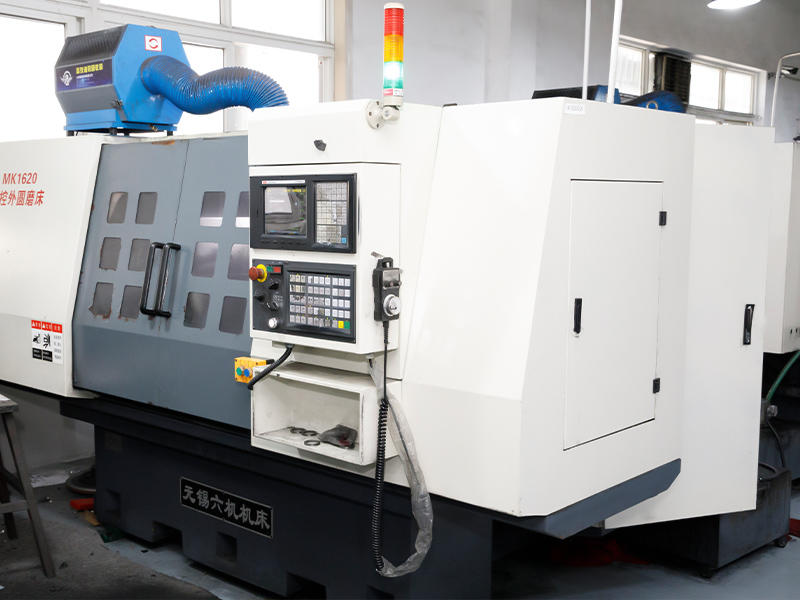
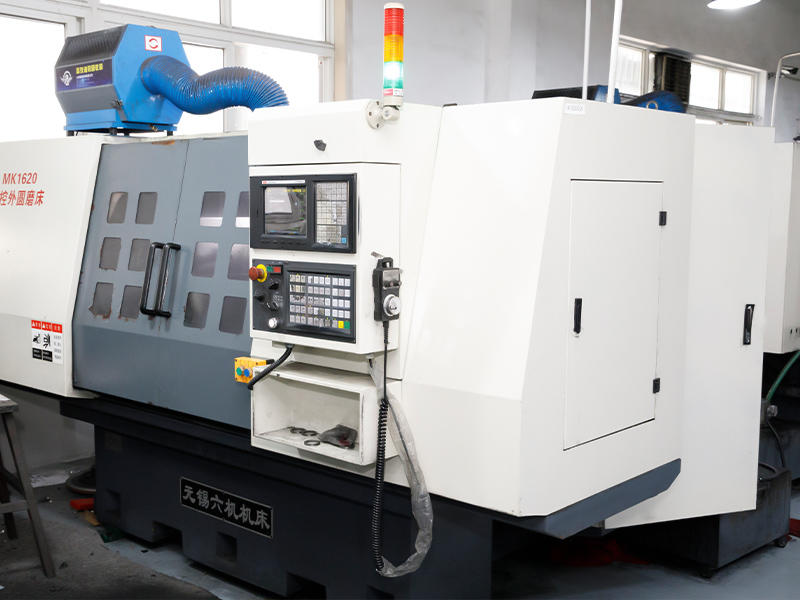