Particle wear-resistant mechanical seal structure for pump The two hard rings at the medium end and the seat are tightly fitted with a heat sleeve, which is beneficial to conduct the frictional heat of the end face to the metal seat 8, so as to reduce the friction on the surface of the sealing pair. temperature. The hard ring of the atmospheric end adopts a floating structure sitting on the O-ring 4, which can avoid thermal cracking caused by the combined effect of the internal stress caused by the interference fit and the friction heat of the end face, such as Elastomer Bellows Seals LSB101 1.2MPa. The two structures have their own characteristics. In any case, it is important to reduce the temperature of the end face of the sealing pair by cooling. To this end, the sealing liquid is circulated and cooled, and cooling water is passed through the inner side of the static ring at the atmospheric end to increase the cooling effect. Here, the following remarks are also required:
①Due to the high operating pressure, the balance structure is adopted on both end faces, and two rings are used for the auxiliary sealing rings of the moving ring and the static ring (seals 5 and 12), which can ensure reliable sealing.
②The push ring 7 and the support ring 6 are divided into two parts (usually as one), which is beneficial to the floating of the moving ring.
③The auxiliary seal ring of the moving ring and the shaft sleeve are relatively static seals, but the axial vibration frequency is high, and the V-ring wears the shaft sleeve greatly, so the contact part of the shaft sleeve is sprayed with ceramic or hard chrome to increase the wear resistance.
④ The static ring clamped by the double O-ring 12 may not be provided with anti-rotation pins.
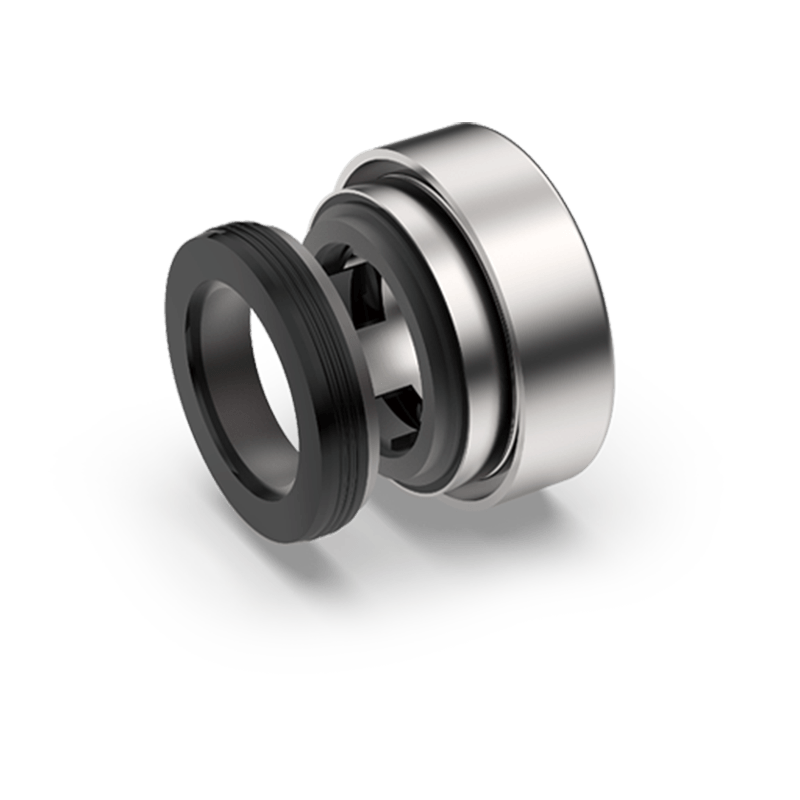
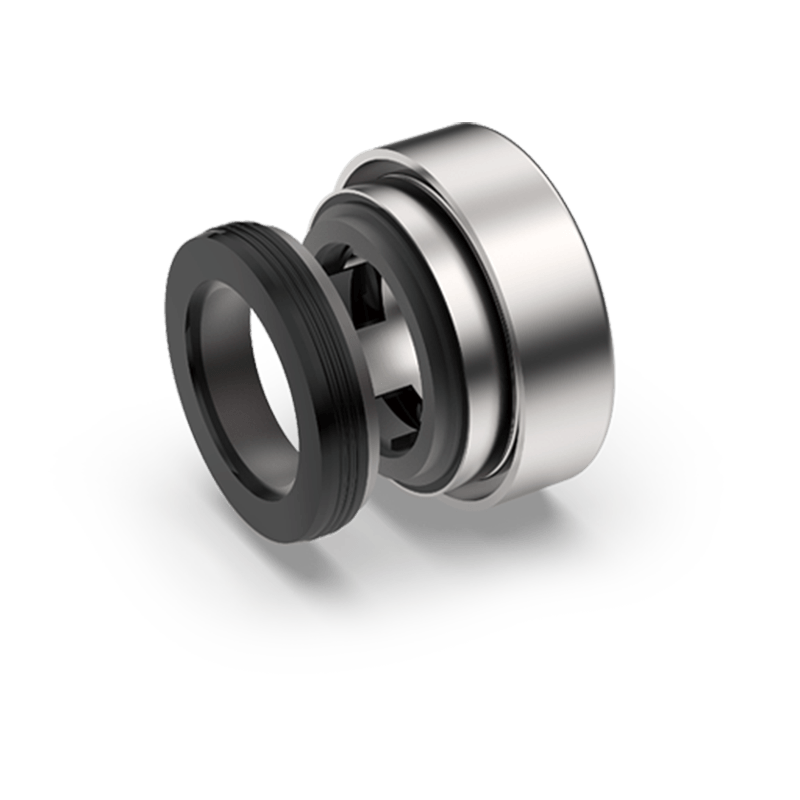