Mechanical seal design points:
For the medium containing high solid particles, the following problems will occur when using ordinary single-end mechanical seals:
①Early wear of friction pair;
②The sliding compensation mechanism is blocked and cannot be displaced axially;
③ Block the loading mechanism to make the elastic element fail;
④Causes wear of rotating components.
In order to solve the above problems, it is necessary to understand the characteristics and operating conditions of the sealing medium in detail, and carry out special design to ensure that its structure, material or sealing system can meet the requirements.
(1) Structural features:
In the design, a structure to prevent the blockage of impurity particles should be adopted, such as an external mechanical seal; when an internal seal is used, the spring should be isolated from the medium. In general, single-face mechanical seals should be preferred because of their low cost and small footprint. However, double mechanical seals must be used in the following situations:
①Solid particle impurities exceed 10wt%;
②Highly concentrated medium;
③ There are dangerous and toxic media;
④ In order to avoid the use of expensive materials in strong corrosive media, etc.
(2) Material of friction pair:
When the structural design and circulation system cannot fully provide the protection of the Silicon Carbide Stationary Seat, the hardness of the selected friction pair material must be higher than that of the abrasive particles. Usually, material pairs with good anti-abrasive wear performance are selected, such as cemented carbide to cemented carbide, carbide to cemented carbide, boron carbide to cemented carbide, etc. When double mechanical seals are used, the material on the atmospheric side can be the same as that used for ordinary mechanical seals.
(3) Sealed circulation system:
When using a single-end mechanical seal, in order to avoid the harm of particulate impurities, measures such as washing, filtration, separation, isolation, heat preservation and heating are taken according to different situations.
When a double-end mechanical seal is used, the sealing liquid is required to generate a relatively high pressure in the sealing cavity for plugging, lubrication and cooling cycles.
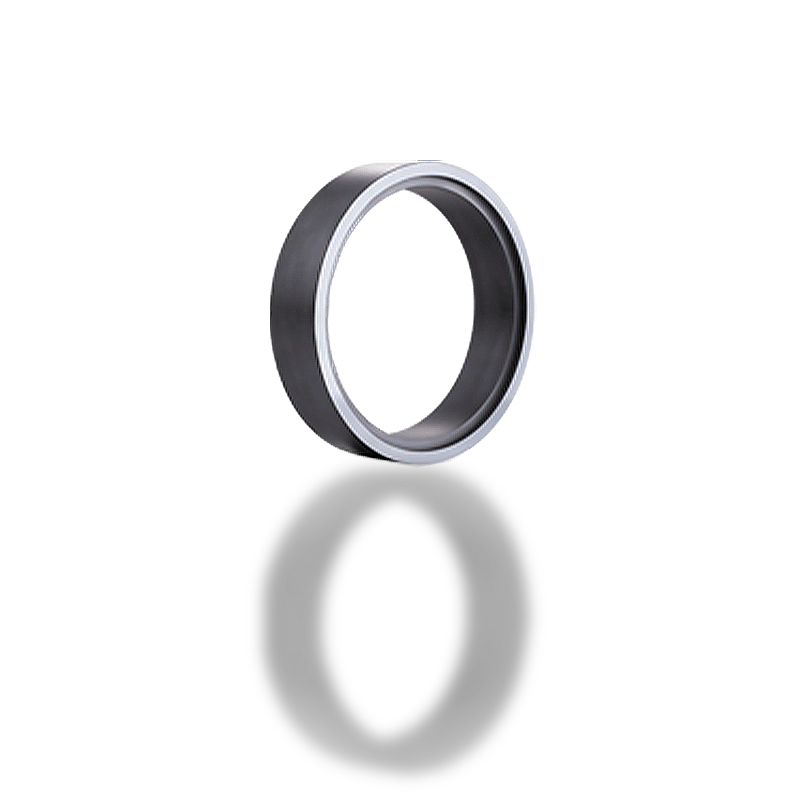
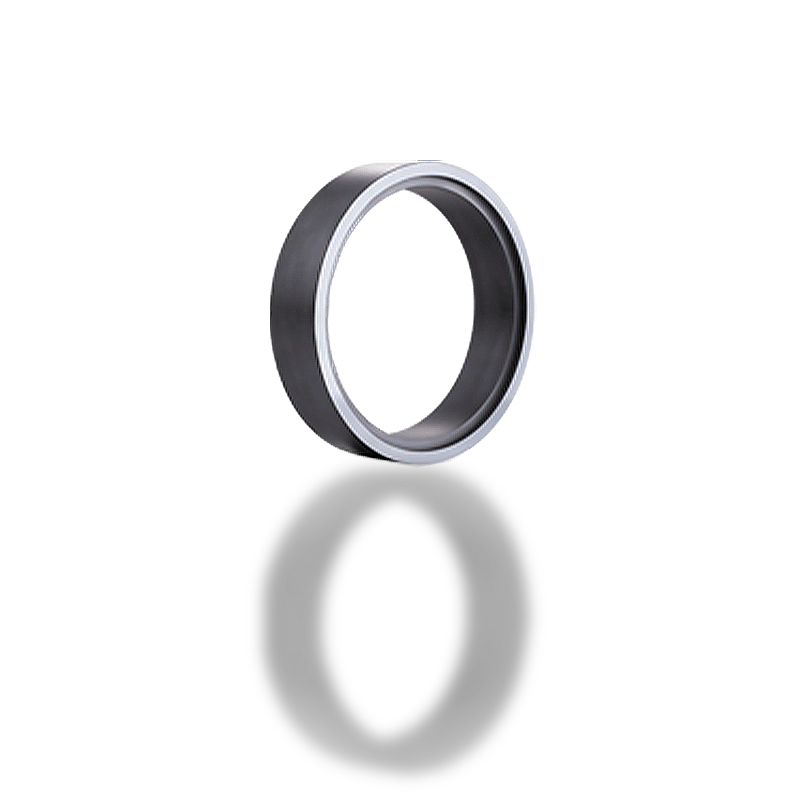