Design considerations for China Custom Tungsten Carbide Seal Rings Manufacturers include:
1.Material Selection: The properties of the tungsten carbide material used for the seal ring, including its hardness, wear resistance, corrosion resistance, and thermal conductivity, should be carefully considered based on the specific application requirements.
2.Seal Configuration: The geometry and configuration of the seal ring, such as its cross-sectional shape, size, and surface finish, should be designed to provide an effective seal and minimize leakage.
3.Pressure and Temperature: The seal ring must be designed to withstand the operating pressure and temperature of the application, including any potential pressure spikes or temperature fluctuations.
4.Lubrication: The seal ring must be lubricated to reduce friction and wear. The type and amount of lubrication required will depend on the specific application.
5.Surface Finish: The surface finish of the seal ring is critical to its performance. The finish should be optimized to minimize leakage while also minimizing wear and damage to the mating surface.
6.Manufacturing Process: The manufacturing process used to produce the seal ring should be carefully considered to ensure consistent quality and reliability.
7.Mating Surface: The mating surface of the seal ring should be considered in the design to ensure compatibility with the mating surface of the application, including any necessary surface treatments or coatings.
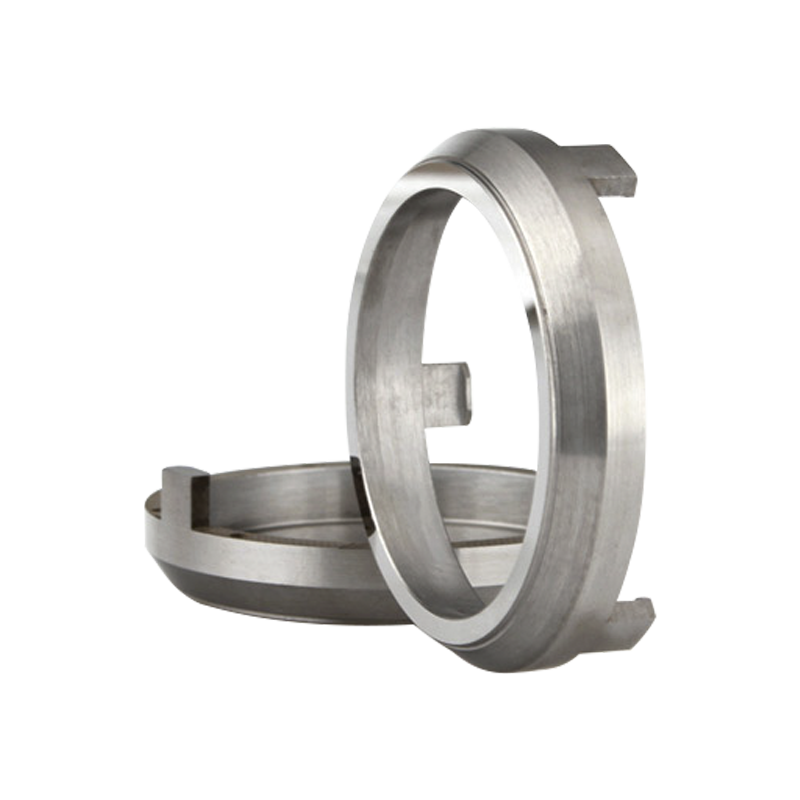
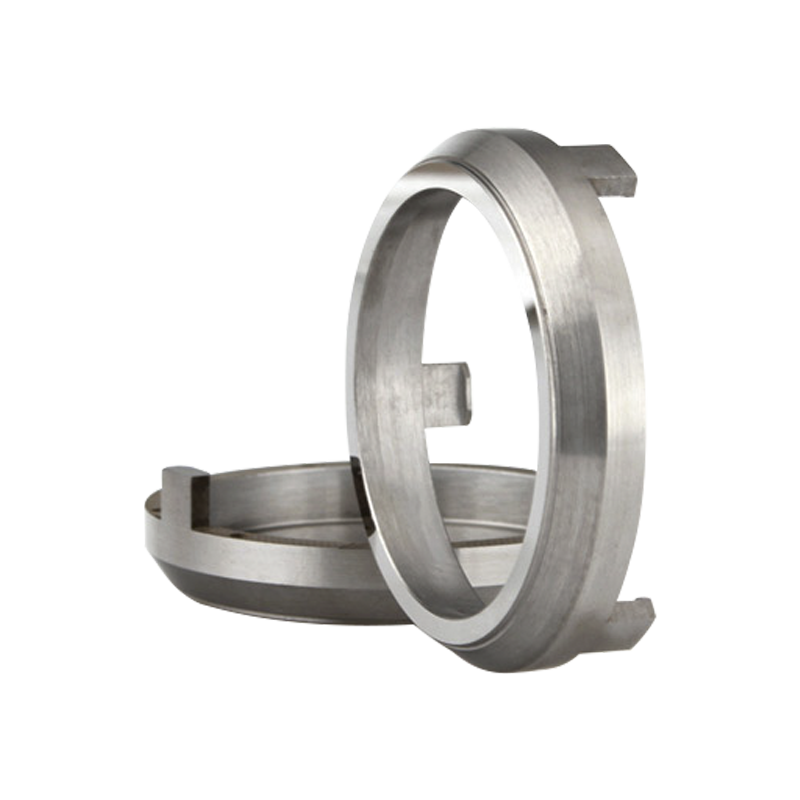
Tungsten carbide is the excellent seal face material in the seal material world. It has high-polished, great wear-resistance, extremely high toughness and corrosion-resistance. Leap Industry can provide Tungsten Carbide(cobalt bonded) and Tungsten Carbide(nickel bonded). All the rings which out diameter from 8mm to 400mm is doable.