Mechanical seals are intricate devices used to prevent fluid leakage in rotating equipment. They consist of various components working together to create an effective sealing arrangement.
Seal Faces:The seal faces are the primary components of mechanical seals that come into direct contact with each other. They are typically made of hard materials like carbon, ceramic, or tungsten carbide, chosen for their wear resistance and compatibility with the fluid being sealed. The seal faces create a dynamic interface that prevents fluid leakage while allowing for the necessary relative motion between the rotating and stationary parts.
Secondary Sealing Elements:Secondary sealing elements, such as O-rings, gaskets, and elastomers, provide additional sealing support and compensate for any face wear or misalignment. These components help maintain proper sealing contact and prevent fluid escape along the seal faces. They are usually made of materials compatible with the fluid and operating conditions, ensuring effective secondary sealing.
Springs:Mechanical seals often incorporate springs to maintain proper face contact and compensate for any axial movement or thermal expansion. Springs provide the necessary loading force to ensure sufficient sealing pressure between the seal faces, thereby maintaining a reliable seal over a range of operating conditions.
Gland and Housing:The gland or housing is the enclosure that holds and supports the mechanical seal assembly. It provides a protective environment for the seal faces and secondary sealing elements, preventing external contaminants from entering and facilitating lubrication. The gland or housing also serves as the connection point between the seal and the equipment, ensuring proper alignment and sealing integrity.
Retaining Rings and Set Screws:Retaining rings and set screws are used to secure the mechanical seal within the equipment. They provide the necessary retention and fixation to prevent the seal from dislodging or rotating during operation. These components ensure that the seal remains in the correct position and alignment, maintaining effective sealing performance.
Flush and Lubrication Systems:In some applications, mechanical seals incorporate flush and lubrication systems. These systems provide a controlled flow of fluid or gas to the seal faces, helping to dissipate heat, flush away contaminants, and maintain proper lubrication. Flush and lubrication systems play a crucial role in enhancing the longevity and performance of mechanical seals, particularly in demanding environments.
Understanding the key components of Mechanical Seals Components Supplier is essential for comprehending their functionality and ensuring effective sealing in rotating equipment. From seal faces and secondary sealing elements to springs, glands, and retaining rings, each component plays a crucial role in creating a reliable and leak-free sealing arrangement. By considering the material selection, proper installation, and maintenance of these components, industries can achieve optimal performance, extended equipment lifespan, and reduced downtime in various applications, including pumps, compressors, and mixers. Mechanical seals continue to evolve with advancements in materials and designs, offering improved reliability, efficiency, and safety in industrial systems.
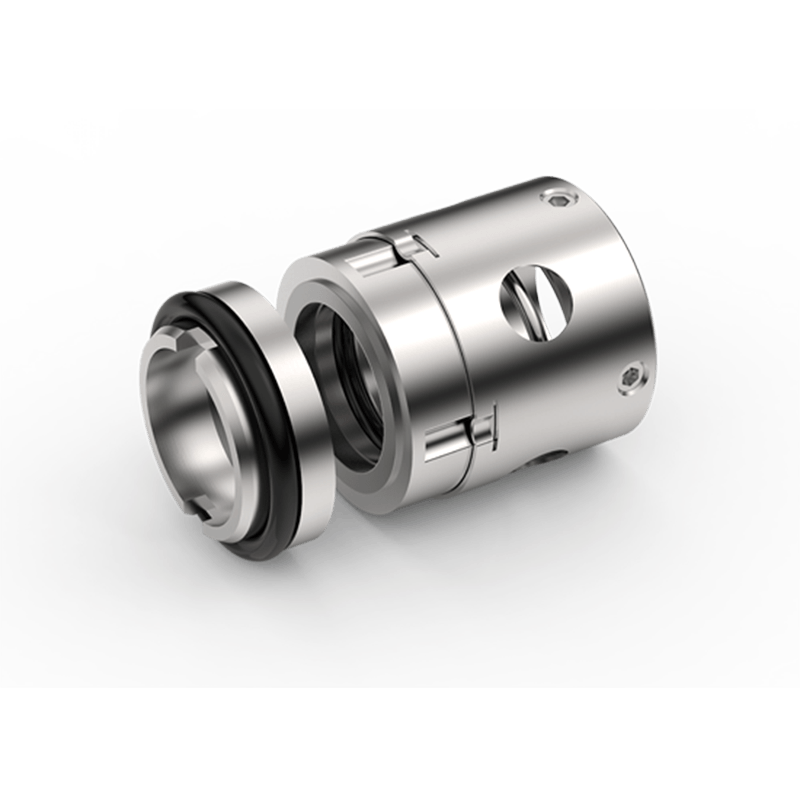
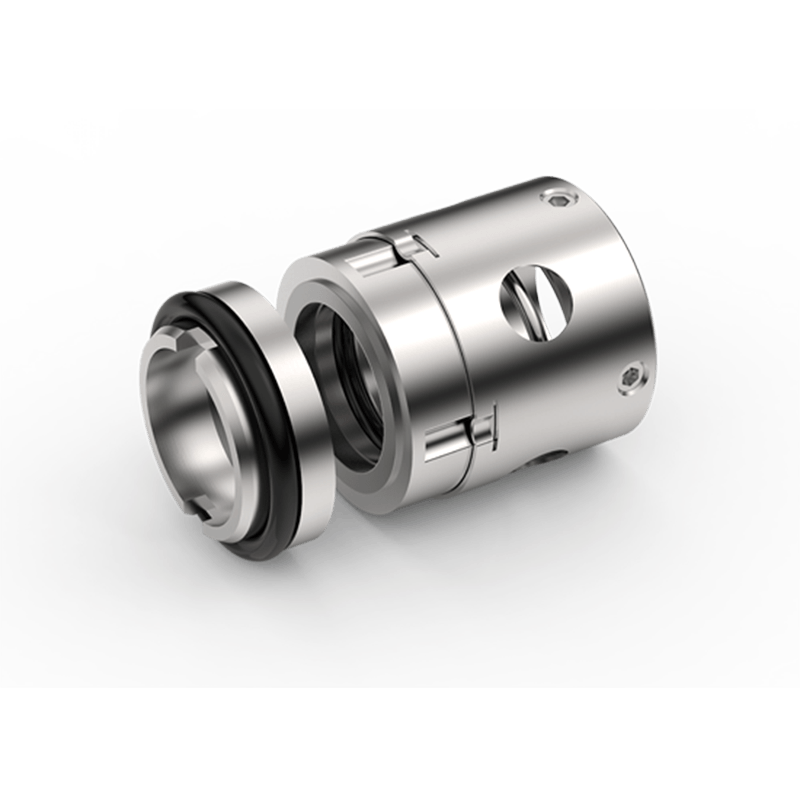
Temperature:-20℃~ +180℃
Rotary Ring:Q1,Q2,U1,U2
Pressure:≤ 1.0MPa
Seat Ring:U2,Q1,Q2,B,A
Speed:≤ 15m/s